A soldering pump is a device commonly referred to as a desoldering pump or solder sucker is compact yet ingenious tool is crafted specifically for the task of efficiently removing molten solder from the joints of a printed circuit board (PCB).
A soldering pump is remarkably straightforward in its design: a spring-loaded piston mechanism within a syringe-like body, geared up to create a vacuum at the nozzle with a simple button press. The resultant suction is powerful enough to draw up the heated, liquefied solder, clearing the way for you to detach or re-seat PCB components with precision. It’s an indispensable addition to any toolkit, bridging the gap between problem and solution in the world of soldering tools.
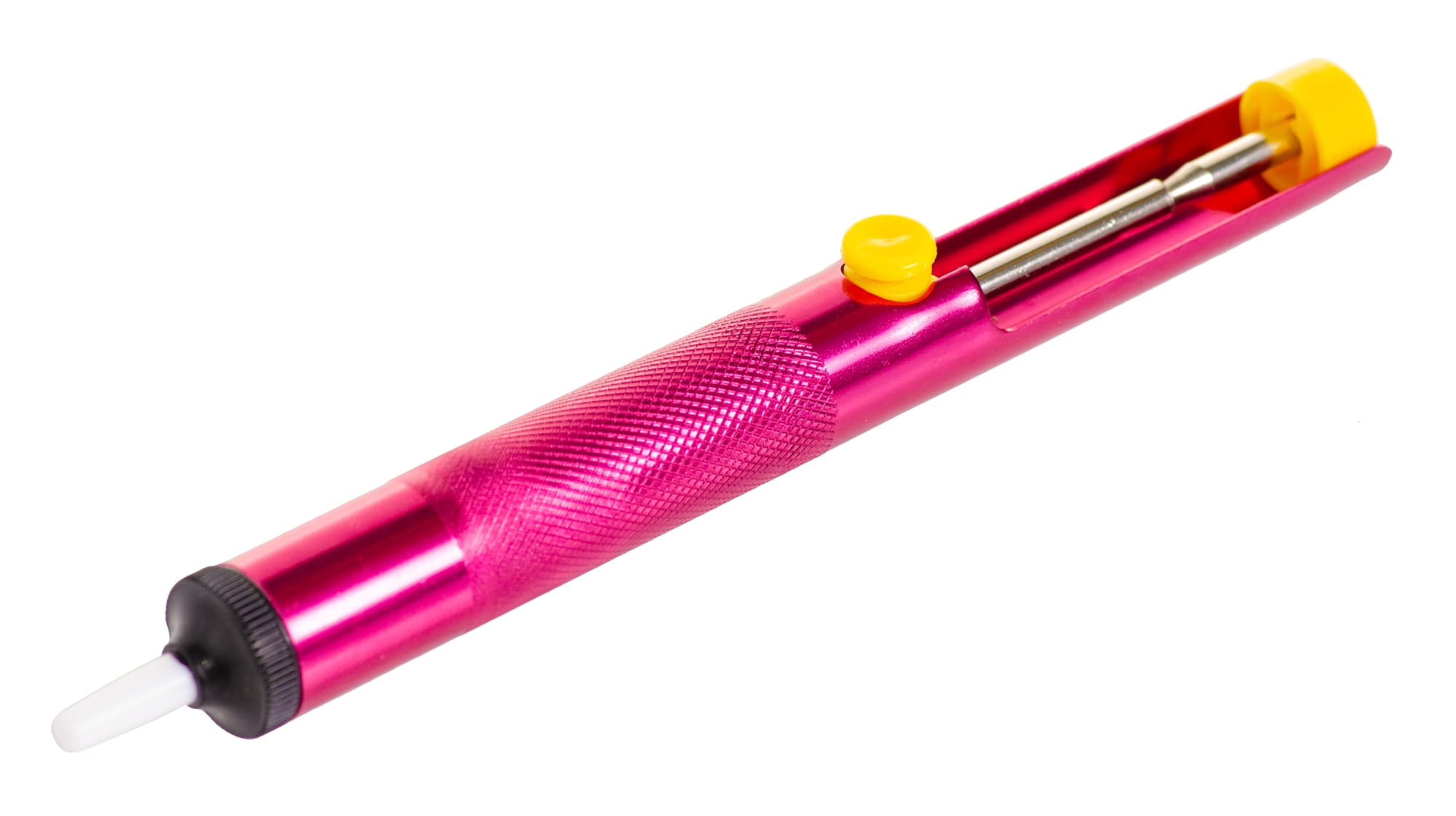
Key Takeaways
- A soldering pump, also known as a desoldering pump or solder sucker, is a primary tool in electronics repair.
- Designed to remove excess or misplaced molten solder, it is a must-have for any soldering toolkit.
- The device operates on a simple piston mechanism, providing strong suction to clear solder efficiently.
- Understanding the proper use of a soldering pump is essential for precise PCB repairs.
- Its role is crucial in the process of detaching and reworking electronic components on circuit boards.
An Introduction to Soldering Pumps
Delving into the world of electronic repairs, one cannot overlook the importance of proficient desoldering techniques, which are often facilitated by the use of a desoldering pump. This handheld device is fundamental in implementing changes or making repairs on a PCB (Printed Circuit Board), offering a solution that combines efficacy with precision. To understand the application and functionality of this vital soldering equipment, we shall explore its structure and role within the domain of soldering and PCB repair.
Defining the Desoldering Pump
At the core of desoldering methodology lies the desoldering pump—an essential tool for any technician engaged in soldering-related tasks. Its simplistic yet functional design consists of a cylindrical body hosting a spring-loaded piston. When the piston is activated, typically by a button-press, it creates a vacuum within the nozzle at the front end of the pump. This vacuum is quintessential in removing the liquefied solder from PCB joints after being heated by a soldering iron, freeing up the electronic components attached thereto.
Significance in PCB Repair and Modification
Illustrating its significance, the desoldering pump stands out as a key player in the process of PCB repair. The precision offered by these pumps aligns perfectly with the intricate requirements of desoldering on PCBs. The pump’s nozzle, being made of heat-resistant plastic, is positioned closely to the molten solder, a move that follows the application of a suitably heated soldering iron to the joint in question. The deployment of the desoldering pump not just facilitates component removal but also ensures the area is prepared for rework or the introduction of new components. The accuracy and cleanliness of this technique make it an indispensable asset in the soldering arsenal.
In summary, the desoldering pump exemplifies an indispensable soldering iron companion, streamlining the desoldering process, a necessary prelude to effective PCB repair or modification.
How a Soldering Pump Enhances the Desoldering Process
In the precision task of electronics repair, the desoldering pump steps into the limelight, taking centre stage in the soldering station repertoire. A celebrity of sorts in the realm of soldering techniques, this device revolutionises solder removal, providing a solution that is both cleaner and more accurate than its counterparts, such as solder wick or braid.
The desoldering pump’s design is tailored to minimise collateral heat damage that may affect neighbouring surface-mounted components during solder extraction. It plays a pivotal role in ensuring that other parts of the circuit remain undisturbed, thereby maintaining the integrity of the PCB during repair or modification.
The desoldering pump’s functionality is not solely limited to solder removal. It goes a step further by protecting adjacent components from the potential heat spillover, a common risk associated with less precise methods. This added layer of protection is why the desoldering pump is an irreplaceable element in any soldering station setup across the United Kingdom.
Tool | Method | Precision | Heat Management |
---|---|---|---|
Desoldering Pump | Vacuum suction | High | Excellent, minimises heat spread |
Solder Wick/Braid | Capillary attraction | Moderate | Good, but requires skilled technique |
Heat Gun | Hot air application | Low | Poor, can affect multiple components |
When contemplating solder removal, it’s evident that the desoldering pump provides a level of finesse unmatched by other tools. Its ability to cleanly void solder from PCB joints without residual debris stands in stark contrast to the alternatives. Thus, it’s not surprising that the desoldering pump is revered as an essential apparatus, primed to assist in any soldering challenge you might encounter.
What is a Soldering Pump and Its Role in Soldering Techniques
When it comes to the meticulous art of soldering, the soldering pump emerges as a critical tool, facilitating the removal of molten solder with remarkable efficiency. This instrument, often sidelined in discussions around soldering equipment, actually plays a cardinal role in the correction and refinement of electronic assemblies. It’s the indispensable ally of the soldering iron, making it possible to rectify soldering mishaps and to modify connections even after the solder has been applied.
Comparing Soldering Pumps to Other Soldering Tools
While a soldering iron applies solder, the soldering pump is tasked with its precise extraction—a symbiosis that balances the addition and subtraction within the soldering ecosystem. Unlike solder wicks or braid, which also remove unwanted solder, the soldering pump operates on a different principle. It uses a suction mechanism to neatly extract molten solder, leaving behind a clean workspace prepped for any necessary rework. This efficiency is unparalleled, especially when working with sensitive electronics where precision is paramount.
In contrast, solder wicks require careful manipulation and can sometimes result in unwanted heat transfer to nearby PCB components. This can lead to collateral damage, whereas the targeted action of a soldering pump minimises this risk. Thus, selecting the appropriate tool for desoldering purposes is not merely a matter of preference but one of ensuring the integrity of the PCB during intricate soldering tasks.
Integration of Soldering Pumps in Soldering Stations
Soldering stations are often equipped with a myriad of tools designed to assist the electronics professional in creating, repairing, and modifying circuits. Among these, a soldering pump is integrated for its specific role in the desoldering phase of the process. Not only does it serve to clear solder from joints with a high degree of precision, but it also lends itself to a variety of soldering tips and strategies that are essential for complex electronic repairs.
The presence of a soldering pump within a well-organised soldering station is indicative of a readiness for any eventuality. It underscores the commitment to quality and detail in soldering work, where each join’s integrity may well determine the overall performance of an electronic device.
The Mechanical Design of a Desoldering Pump
The internal mechanics of a desoldering pump are an elegant testament to the ingenuity behind soldering equipment mechanics. Eschewing complexity for simplicity and reliability, the design underpinning this tool is as ingenious as it is imperative for any electronic repair task. Here we unpack the meticulous engineering that allows a soldering pump to perform with such impressive efficiency and ease.
Understanding the Internal Structure of a Soldering Pump
At first glance, a desoldering pump might seem unassuming. However, within its cylindrical body lies a concert of components harmonised for a singular purpose: precise extraction of molten solder. The internal assembly includes a spring, a lever, a piston, and a mechanical lock, all enclosed within what is commonly known as a syringe-like body. This compact design is key to its functionality in the soldering equipment canon.
The nozzle, diligently crafted from heat-resistant plastic, is not only built to withstand high temperatures during desoldering operations but also designed to prevent the solidification and subsequent blockage of extracted solder. Such a careful consideration in the soldering pump design offers a glimpse into the meticulous attention to detail advocating for the pump’s utility and durability.
The Functionality of Pump Head and Piston Mechanisms
Central to the desoldering pump’s operation is the piston mechanism—a marvel of soldering equipment mechanics. Primed by a spring, the piston awaits activation by way of a convenient button. Upon pressing, the mechanism leaps into action, and the piston swiftly retreats, inducing a vacuum at the pump head. This split-second transition from stasis to motion culminates in the solder being rapidly drawn into the pump, from where it can be discarded easily.
Such swift and effective removal of solder is made possible through meticulous engineering that ensures seamless movement and airtight sealing within the pump. It holds true that good design is often invisible, and with each activation of a desoldering pump, the unassuming genius of its mechanics is quietly reaffirmed.
Understanding the internal structure and mechanics of a desoldering pump is crucial for anyone looking to employ such a device in their soldering repertoire. As we’ve seen, the design and functionality of these indispensable tools marry simplicity with high performance, reflecting the soldering pump’s vital role in the world of soldering equipment.
Step-by-Step Guide: How to Use a Soldering Pump Effectively
To adeptly manoeuvre through the intricacies of soldering station maintenance and utilise a soldering pump to its full potential, one must adhere to a structured approach. This guide aims to illuminate the methodical steps essential for effectively leveraging this vital tool within your soldering repertoire.
Priming the Desoldering Pump
The initial step in how to use a soldering pump involves the fundamental act of priming. Beginning with a firm grasp, depress the plunger of the desoldering pump until you sense it securely lock into position. This action primes the internal spring, preparing your soldering pump for the desoldering procedure ahead.
Deploying the Solder Sucker During Desoldering
Having successfully primed your tool, focus on the solder joint you aim to clear. Once the solder has reached a molten state, introduce the nozzle of the solder pump as close to the liquified solder as feasible without causing damage to the pump itself, thanks to its heat-resistant plastic design. Employing the black side button, activate the pump, which invitingly sucks the molten solder into its chamber. If the joint remains uncleared, repeat the process or complement it with solder wick for meticulous cleaning.
Cleaning and Maintaining Your Soldering Equipment
Post-desoldering, your soldering pump might host residual solder within its confines. Adequate soldering station maintenance calls for immediate cleaning to prevent blockage. Engage the pump’s mechanism multiple times to propel any remaining solder through the nozzle. For a thorough cleanse, disassemble by unscrewing the nozzle and meticulously remove any lingering solder from the interior.
Consistent and correct maintenance of your soldering equipment not only prolongs its lifespan but also ensures steadfast performance in all your soldering endeavours. With these soldering tips at your disposal, mastering the use of a soldering pump shall no longer be an enigma but rather a testament to your prowess in electronic repairs.
Precautions and Best Practices with Soldering Pumps
Embracing soldering safety is not just about following guidelines; it’s about embedding best practices into every aspect of desoldering pump usage. Whether you are a seasoned professional or a novice starting out, understanding the dynamics of safe soldering is imperative. The following are the precautions and best practices meticulously designed to bolster safety and proficiency in handling soldering pumps within the United Kingdom’s electronic repair landscape.
Bracing Against Kickback: A Must for Stability
To negate the substantial kickback experienced whilst activating a desoldering pump, it’s paramount to secure the device with a steady grip. Brace your hand firmly to ensure that the nozzle remains stable. This not only contributes to precise solder removal but also prevents mishaps that may arise due to sudden movement.
Heat Management Near SMT Components
When working in proximity to diminutive surface-mounted components (SMT), special caution must be exercised. The conjunction of heat and suction produced during the desoldering process may inadvertently dislodge these sensitive parts. It is advisable to avoid using the pump near such components altogether or to adopt a gentler approach if necessary.
- Before engaging with the pump, familiarise yourself by activating it a few times to understand the release mechanism.
- Compress the plunger until it clicks into a locked position, readying the pump for action.
- When the solder is sufficiently molten, position the nozzle as near as possible without touching the PCB directly.
- Activate the pump using the designated button, ensuring the molten solder is promptly and effectively extracted.
- For a thorough clean, you may have to repeat the process. Continual learning and application of these steps will cement them into your soldering best practices repertoire.
Cleaning: Pivotal to Pump Longevity
Cleaning the desoldering pump is a staple in soldering station maintenance. After use, expel any residual solder by activating the pump a few more times. Should a deeper clean be in order, carefully disassemble the nozzle and attend to any solder accumulation within. This kind of diligent upkeep not only extends the pump’s lifespan but also ensures optimal performance consistent with soldering best practices.
By embracing these safety measures and using a desoldering pump in accordance with best practices, you fortify your soldering activities against potential risks, thereby ensuring safety, precision, and longevity in all your soldering projects.
Understanding Desoldering: Removal of Components from PCBs
In the meticulous realm of circuit repair and PCB modification, the act of desoldering is as critical as the initial soldering itself. Desoldering is not simply the reverse of soldering; it’s an art that requires precision, patience, and the right desoldering techniques. Here, we delve into the complex yet fascinating process of removing solder from PCBs to either rectify defective circuits or make way for new components.
The Crucial Role of Desoldering in Circuit Repair
The unwavering companionship between the soldering pump and the technician is emblematic of the paramount importance desoldering holds in electronics. Whether addressing a flawed circuit connection or upgrading to sophisticated parts, the elimination of existing solder stands as a gateway to circuit innovation and restoration. This is where the elegance of a well-executed desoldering technique shines, safeguarding the functionality of the board while paving the way for enhancements.
Desoldering Techniques: Utilising the Desoldering Pump and Solder Wick
To accomplish a pristine joint ready for a new solder application, the soldering pump is employed. This tool is synonymous with efficiency and is often the first line of action when it’s time to replace or reposition components. However, for those occasions when tenacious solder remains, the use of a solder wick is recommended. This paired approach ensures a comprehensively clean site, crucial for high-quality repairs and modifications.
- Priming Your Soldering Pump: Before any desoldering begins, ensure your soldering pump is in ready condition. Familiarising oneself with the tool’s function by engaging the pump a few times is a wise start.
- Working with the Solder Wick: After the majority of the solder is suctioned off by the pump, press the solder wick against the joint and heat it with the iron to soak up residual solder, thus ensuring a thorough clean-up.
Proper understanding and application of these desoldering methods are quintessential for any technician involved with PCB repairs. By mastering these desoldering techniques, one can navigate the complexities of circuit repair with confidence and precision. The desoldering pump, alongside its trusted ally, the solder wick, are indispensable tools in the pursuit of PCB perfection.
Different Types of Soldering Pumps and Their Applications
In the specialised space of PCB repairs and modifications, discerning the right soldering pump types becomes essential. Desoldering equipment is not a one-size-fits-all affair; rather, it’s about selecting the tool that’s most fitting for the task at hand. Generally speaking, the two most prevalent varieties are the plunger-style and bulb-style solder suckers, each with specific advantages tailored to different requirements.
The plunger-style solder sucker is favoured for its rapid action, making it a valuable asset when working within ample space. Its robust suction capability and efficiency make it a go-to choice for professionals who work with desoldering equipment on a regular basis in the United Kingdom. On the flip side, the bulb-style solder sucker’s compact stature and straightforward design make it an ideal companion for tackling constricted spaces or for those seeking a more portable solution.
Choosing between these soldering pump types depends on the unique design demands of the PCB in question, and the nature of the repair or adaptation necessary. While the plunger-style affords speed and strength, the bulb-style’s simplicity and manoeuvrability present it as a capable contender for the meticulous work of desoldering in tight quarters. Ultimately, having knowledge of and access to both types ensures that technicians are well-equipped to address a breadth of desoldering tasks with aptitude and agility.